Careers
At HAT Design Works, we foster an environment of teamwork, creativity, continuous improvement and respect and integrity. We strive to create opportunities for growth and development of a committed, engaged workforce focused on the highest levels of customer satisfaction.
We’re always looking for new talent to join the HAT team. If you’re interested in bringing your skills to HAT Design Works, please send your resume for review. Qualified applicants will receive consideration for employment without regard to race, color, religion, sex, national origin, sexual orientation, gender identity, disability or protected veteran status.
Discover the Lehigh Valley
Live. Work. Play.
Not only do we think we’ve got the best corporate culture around, we think we’re located in one of the best locations around. Whether you enjoy mountains, beaches, or the excitement of a large cosmopolitan city, you can have it all in the Lehigh Valley. We’re centrally located within one hour of the Pocono Mountains and the New Jersey shore, and we’re just a short drive to New York City or Philadelphia. We’ve gathered a few highlights to give you a taste as to why the Lehigh Valley is a great place to live, work and play.
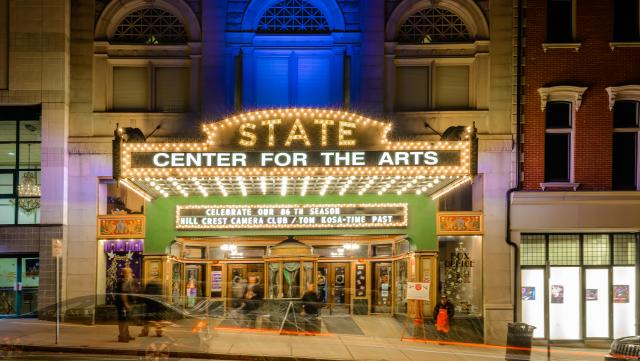
Credit: Discover Lehigh Valley®
State Theatre Center
for the Arts
An eclectic group of shows will entice audiences to Easton’s State Theatre, which celebrated its 90th anniversary in 2016. Originally opening on the BF Keith vaudeville circuit in 1926, today the Theatre continues to present top headliners, national tour Broadway shows, comedy, concerts, family programming, and more.
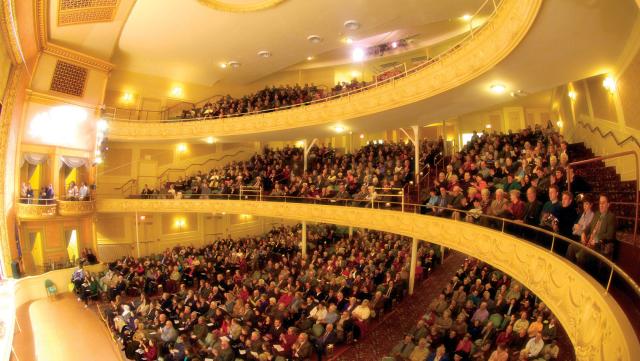
Credit: Discover Lehigh Valley®
Miller Symphony Hall
The historically significant, 1,200-seat Miller Symphony Hall is a premier performing arts facility in Allentown and host to Lehigh Valley’s only professional orchestra, having celebrated its 65th anniversary season in 2015.
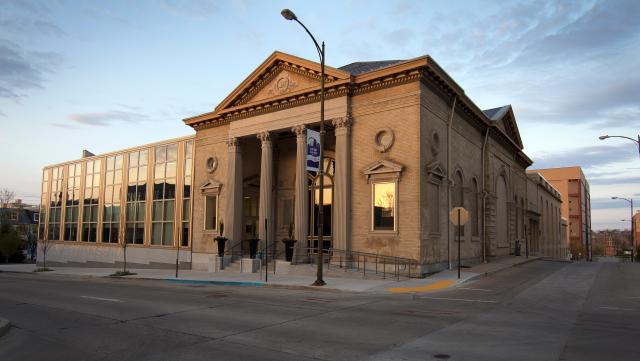
Credit: Discover Lehigh Valley®
Allentown Art Museum
The Allentown Art Museum is a vibrant cultural center with a world-class collection, programs for visitors of all ages, and a distinctive museum store.
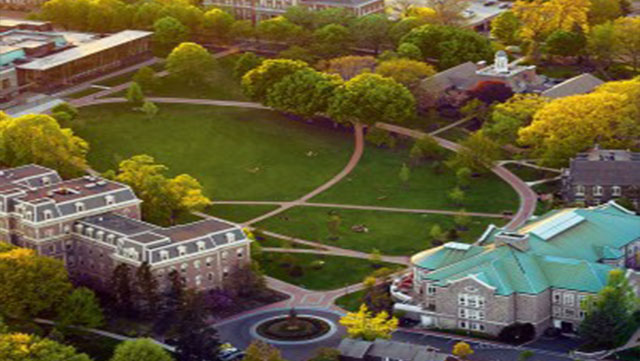
Credit: Discover Lehigh Valley®
Lafayette College
Lafayette College is a private liberal arts college based in Easton, Pennsylvania with a small satellite campus in New York City. Founded in 1826 by James Madison Porter and the citizens of Easton, the school first held classes in 1832.
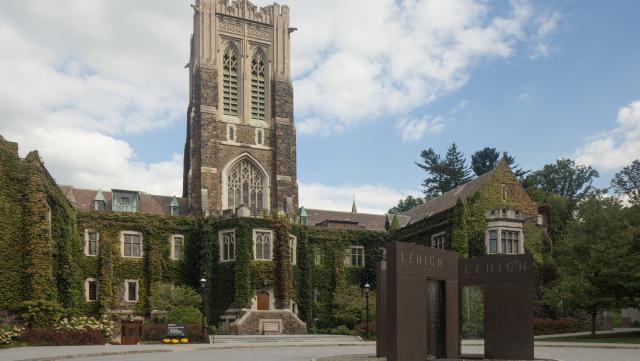
Credit: Discover Lehigh Valley®
Lehigh University
Lehigh University is a private research university in Bethlehem, Pennsylvania. It was established in 1865 by businessman Asa Packer. Lehigh offers world-class academic opportunities on one of the nation’s most beautiful campuses.
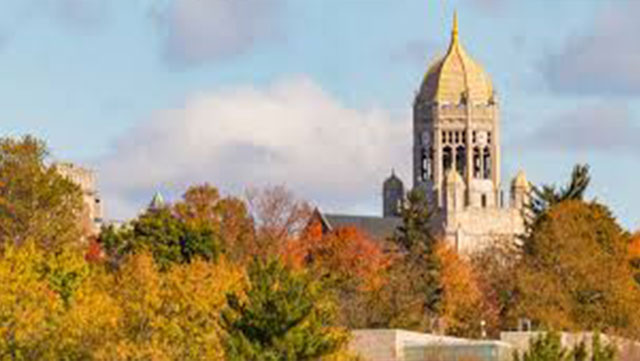
Credit: Discover Lehigh Valley®
Muhlenberg College
Muhlenberg is a highly rated private, Christian college located in Allentown, Pennsylvania. It is a small institution with an enrollment of 2,279 undergraduate students.
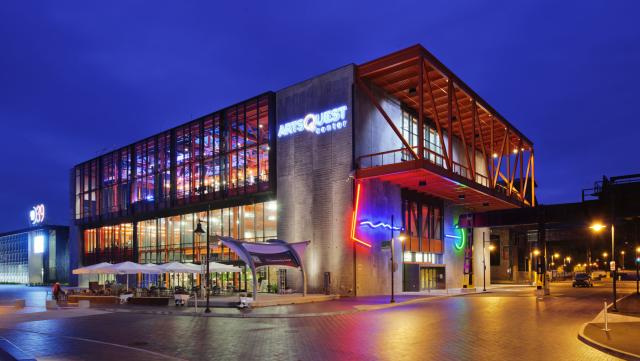
Credit: Discover Lehigh Valley®
ArtsQuest™ Center at SteelStacks™
The ArtsQuest™ Center is a dynamic, multi-use performing arts center set amidst the 10-acre SteelStacks™ campus located on the former Bethlehem Steel plant property in south Bethlehem.
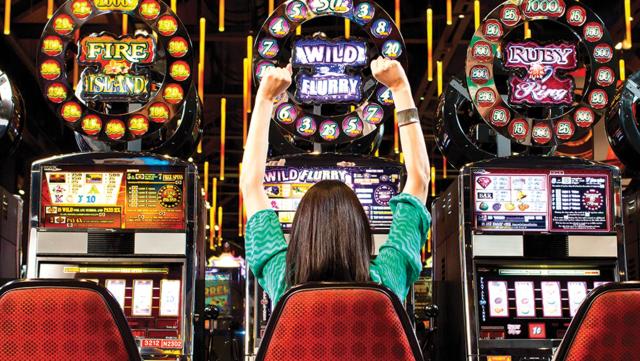
Credit: Discover Lehigh Valley®
The Casino at Wind Creek Bethlehem
Wind Creek Bethlehem Casino offers over 3,000 state-of the-art slot machines. Live dealer stadium gaming is now open at Wind Creek Bethlehem Casino. Play low- limit, live dealer baccarat and roulette at your own pace without a table full of other players, with the opportunity to win big!
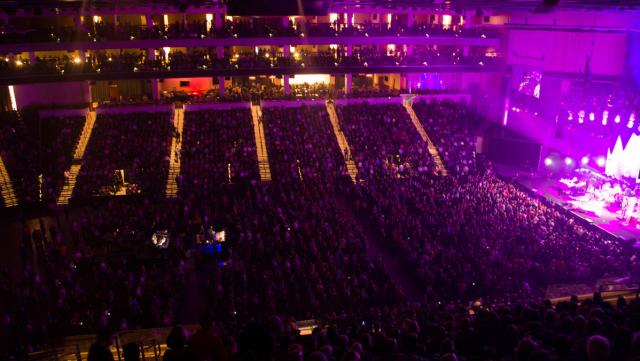
Credit: Discover Lehigh Valley®
PPL Center
PPL Center is a state-of-the-art multipurpose arena in downtown Allentown, Pa. The arena seats more than 10,000 for concerts and more than 8,500 for Phantoms professional hockey games, making it the region’s largest events venue.
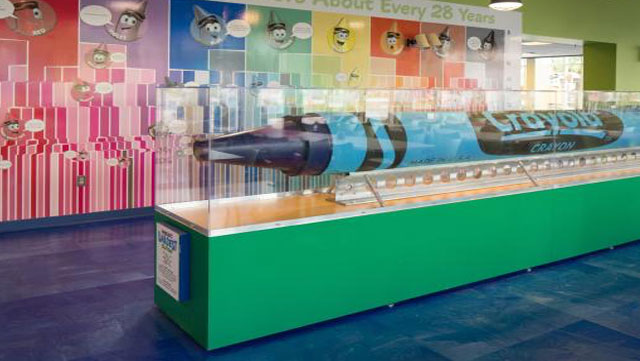
Credit: Discover Lehigh Valley®
Crayola Experience™
Discover the magic of color at Crayola Experience, Crayola’s premier, one-of-a-kind family attraction! Dozens of hands-on, creative activities and a full day of fun awaits families in Easton.
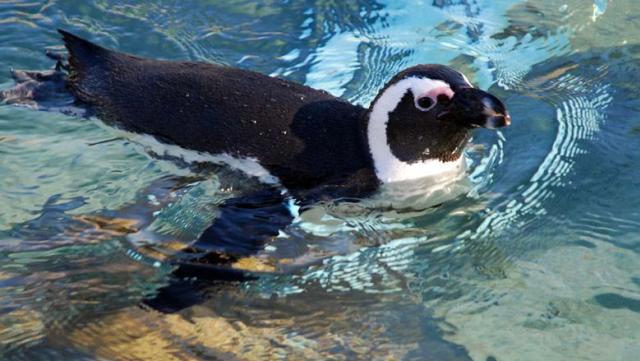
Credit: Discover Lehigh Valley®
Lehigh Valley Zoo
Home to more than 300 animals representing over 100 species, the Lehigh Valley Zoo offers unforgettable and memorable visits among wildlife and nature.
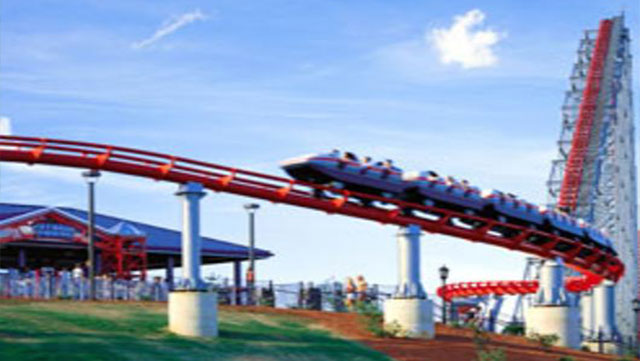
Credit: Discover Lehigh Valley®
Dorney Park + Wild Water Kingdom
Lehigh Valley’s Dorney Park & Wildwater Kingdom features two great parks for the price of one, spread across 200 acres of amusement! There are more than 100 rides, shows and attractions for guests to enjoy including seven roller coasters, the largest collection of kids’ rides in Planet Snoopy™ and one of the country’s best-ranked water parks.
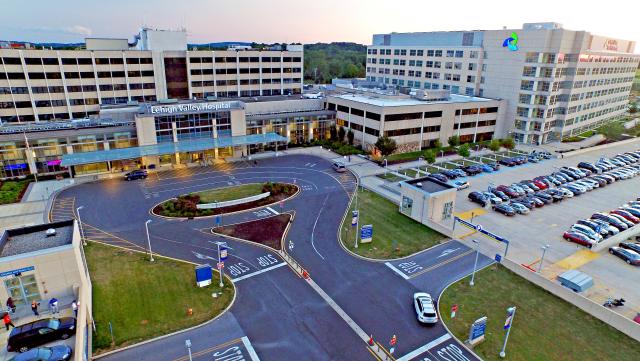
Credit: Discover Lehigh Valley®
Lehigh Valley Health Network
Lehigh Valley Health Network has been recognized by U.S. News & World Report Opens in New Window for 22 consecutive years as one of America’s Best Hospitals. Each one of the more than 17,000 colleagues contributes to this mission and helps make the Lehigh Valley a healthier – and better – place in which to live.
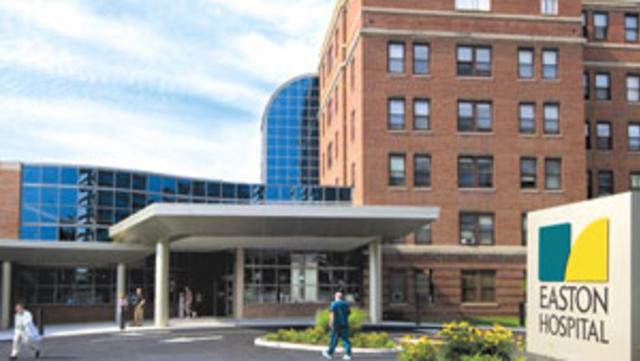
Credit: Discover Lehigh Valley®
Easton Hospital
Easton Hospital is your community healthcare provider. We’re 1,351 healthcare professionals strong and believe in the power of people to create great care.
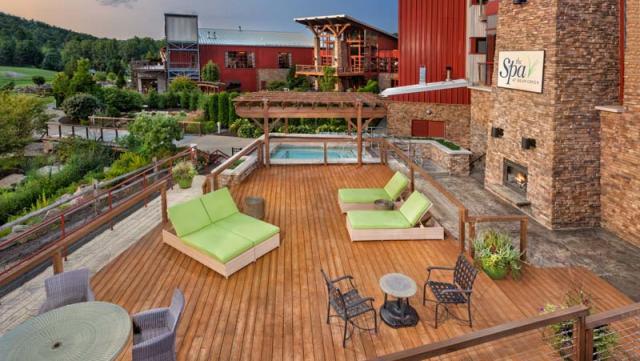
Credit: Discover Lehigh Valley®
The Spa at Bear Creek
Skiing isn’t the only way to get a “lift” when at Bear Creek. The Spa at Bear Creek awaits to rejuvenate you. The Day Spa is open to non-resort guests and offers body wraps and treatments, facials, massages, nail treatments, a full-service kids and teen spa, and a hair salon.
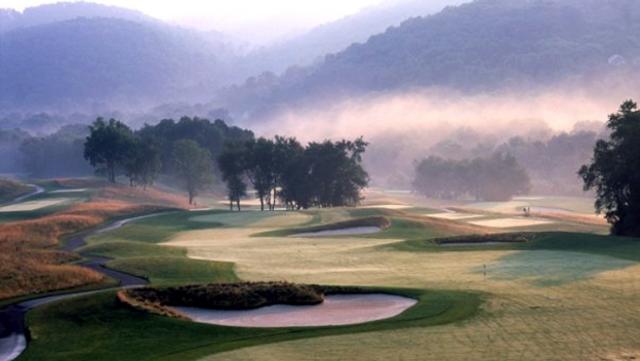
Credit: Discover Lehigh Valley®
The Architects Golf Club
In 2001, owners Dennis and Lawrence Turco had a vision to open one of the most renowned golf courses in the world – one that paid tribute to the great design styles of the game’s most prolific architects.
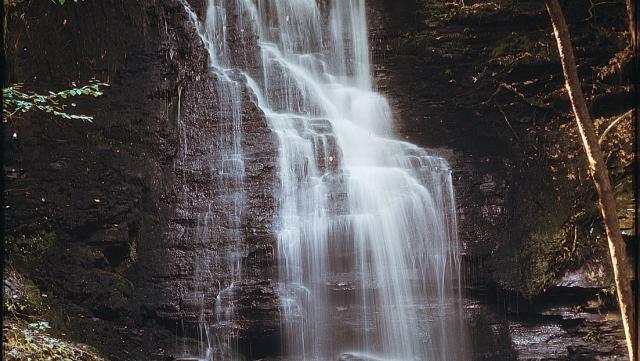
Credit: Discover Lehigh Valley®
Bushkill Falls
The “Niagara of Pennsylvania”, Bushkill Falls is among the Keystone State’s most famous scenic attractions. This unique series of eight waterfalls nestled deep in the wooded Pocono Mountains just outside Lehigh Valley, Pa. is accessible through an excellent network of hiking trails and bridges which afford fabulous views.
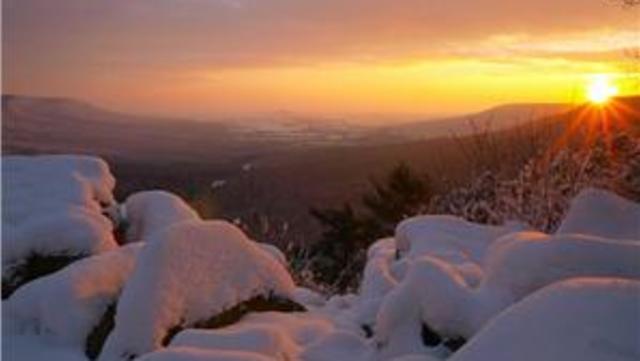
Credit: Discover Lehigh Valley®
Hawk Mountain Sanctuary
Lehigh Valley’s Hawk Mountain Sanctuary is a wild bird sanctuary located along the Appalachian flyway. It’s an outdoor destination for hikers, birdwatchers and outdoor enthusiasts alike.
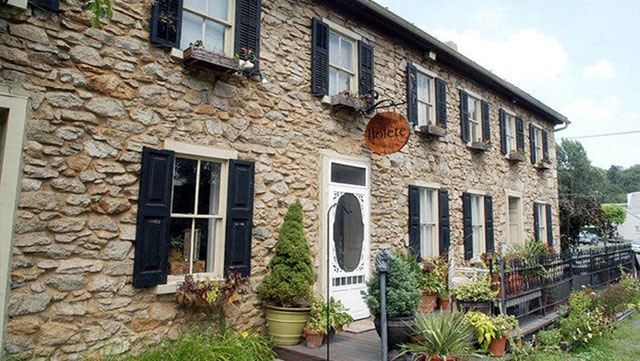
Bolete
One of the top rated restaurants around offers a rustic-chic destination serving a seasonal farm-to-table menu of American cuisine, with a full bar.
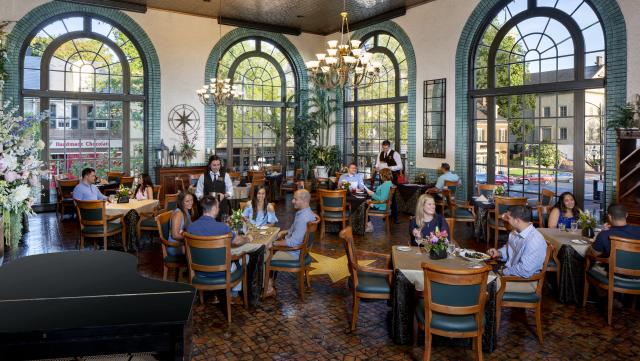
Credit: Discover Lehigh Valley®
1741 on the Terrace
Try something new or revisit something familiar but above all — enjoy. Relax in the ambiance of the garden atmosphere of the hotel’s original solarium design with Moravian tile floor and soaring Palladian windows.
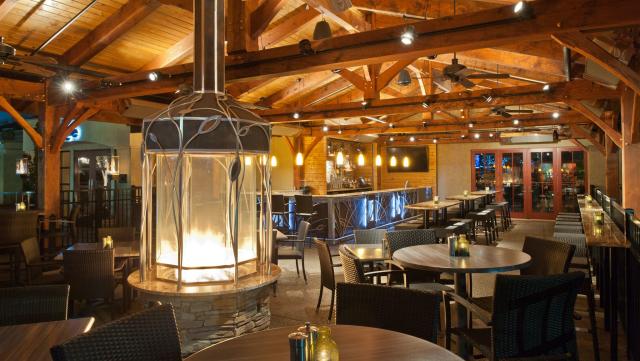
Credit: Discover Lehigh Valley®
Blue Grillhouse
When blue opened in 2002, it instantly became one of Lehigh Valley’s premier fine dining establishments. Its stylish ambiance was a departure from conventional steakhouses, while the food, service, and extensive wine list impressed even the most discerning diners.
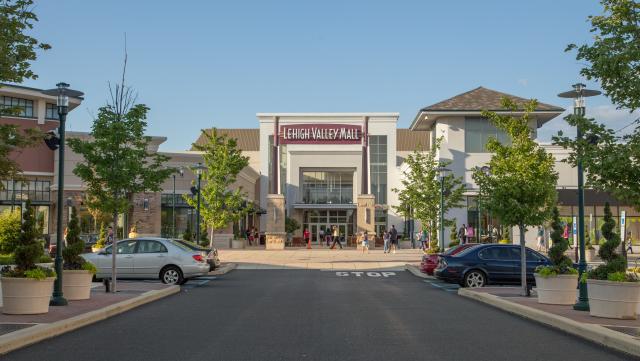
Credit: Discover Lehigh Valley®
Lehigh Valley Mall
Featuring over 150 stores and restaurants, Lehigh Valley Mall is the premier shopping destination in the greater Allentown, Bethlehem, and Easton markets.
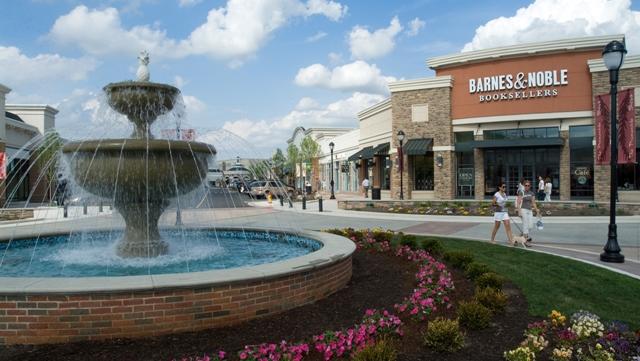
Credit: Discover Lehigh Valley®
The Promenade Shops at Saucon Valley
The Promenade Shops at Saucon Valley Opens in New Window is the area’s only outdoor Lifestyle Center, and is nestled at the base of South Mountain on Center Valley Parkway between Allentown and Bethlehem.
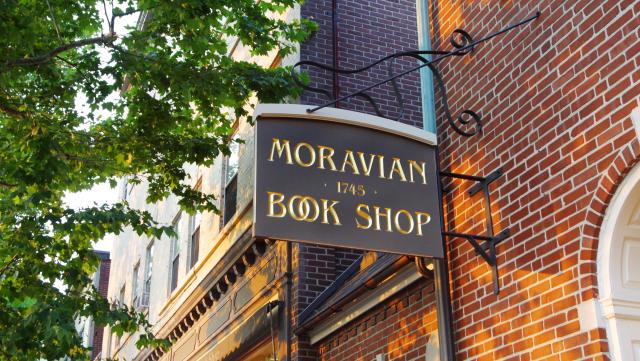
Credit: Discover Lehigh Valley®
Moravian Book Shop
The Moravian Book Shop is the oldest continuously running bookstore in the world. Established in 1745 on the south side of the Lehigh River, the Moravian Book Shop resided in several locations before moving to its current site in the heart of historic downtown Bethlehem in 1871.
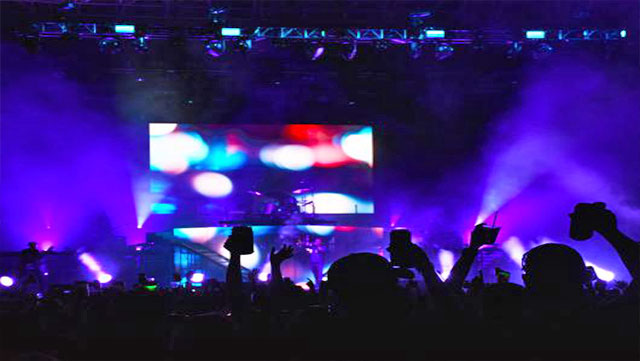
Credit: Discover Lehigh Valley®
Musikfest®
Each August, Bethlehem’s historic downtown comes alive in a kaleidoscope of sensational sounds as Musikfest® welcomes more than 450 performers to Lehigh Valley for 10 days of nonstop music.
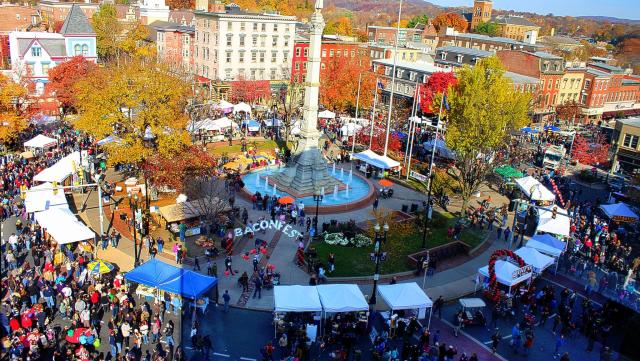
Credit: Discover Lehigh Valley®
PA Bacon Fest
Located in historic Easton, the PA Bacon Fest has grown into one of the region’s most popular events. With 150+ vendors, 12+ musical acts, and several stages, the two-day festival is a must-see for food lovers.
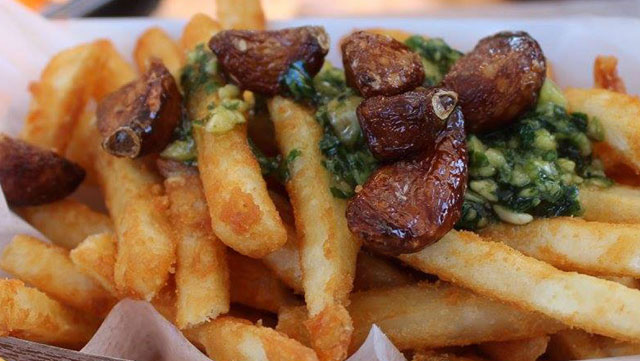
Easton Garlic Fest
More than 90 vendors including merchandise and crafters, prepared foods, packaged foods, garlic vendors, and service providers.
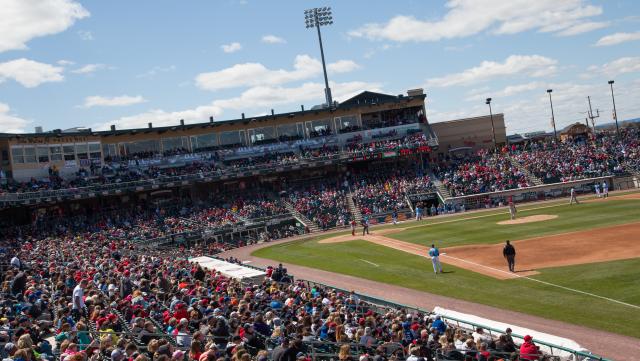
Credit: Discover Lehigh Valley®
Lehigh Valley IronPigs Baseball
Since debuting in 2008, the Lehigh Valley IronPigs have led Minor League Baseball in per game attendance at Coca-Cola Park with 10,100 capacity and has become the Lehigh Valley’s place for affordable family entertainment.
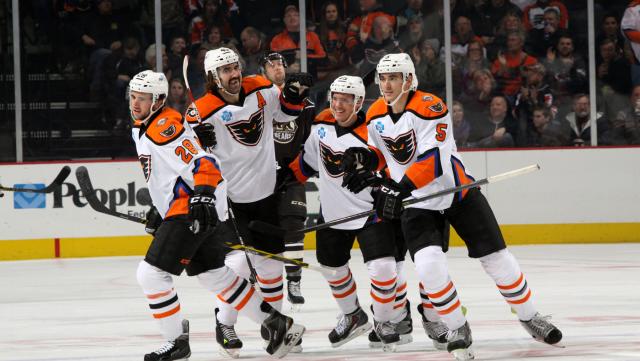
Credit: Discover Lehigh Valley®
Lehigh Valley Phantoms Hockey
The Lehigh Valley Phantoms, proud American Hockey League (AHL) affiliate of the Philadelphia Flyers, are coming off an incredibly successful season playing at the PPL Center.
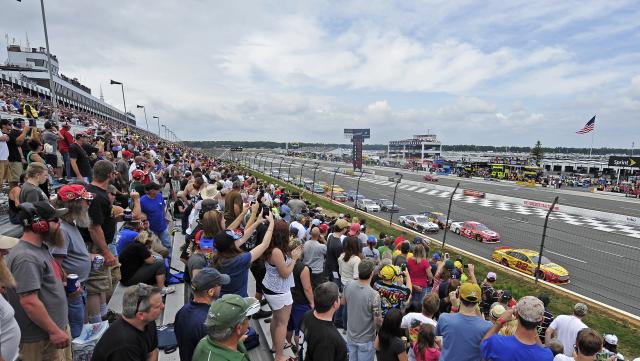
Credit: Discover Lehigh Valley®
Pocono Raceway
Pocono Raceway: A spectacular sport venue with a focus on NASCAR races. Pocono Raceway provides a family-friendly experience at a great value. The track, otherwise known as the “Tricky Triangle,” is one of the most unique racetracks out there, with the longest front-stretch in motorsports and three distinct turns.